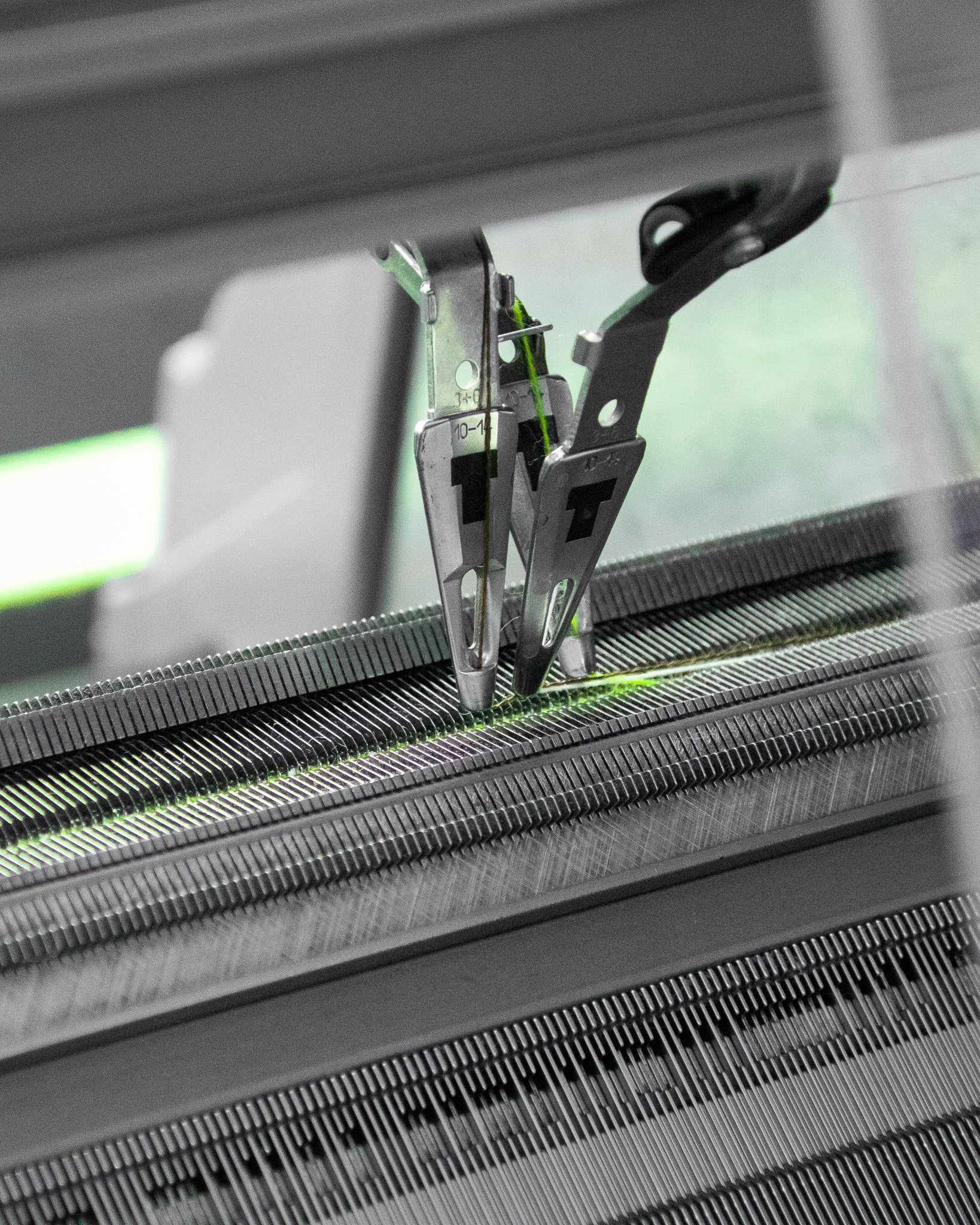
Zero-Waste Jacket
Fabric and garment design integration.
Structure Mapping
For An Overcoat
A patent-pending technique for 3D circular knitting.
Shaping fabric in the production stage affords designers more freedom in designing a material-efficient garment pattern. It also enables the transformation of non-zero-waste patterns into zero-waste.
This project demonstrates that transformation process.
Step 1: Concept
Intention
A true archetype of clothing. The overcoat has proven to be a timeless design and thus serves perfectly as a demonstrator for a new production and design method.
Step 2: Technical Developent
Pattern Making
The standard pattern for an overcoat is somewhat common knowledge. Therefore, most attention went to perfecting the fit to a custom digital model.
CAD in CLO3D
To optimise the fit of the jacket to a personalised avatar, I used CLO3D and the Avatar Editor and adjusted the pattern to fit the shoulders, back, and collar.
Step 3: Structure Mapping
Patent Pending.
Simplification
The first step to structure mapping is simplification. Abstracting complex curved parts to rectangular segments, roughly the size of the original elements.
Additionally, some elements can be combined, knowing those seams can be recreated during the fabric production process.
Zero-Waste Pattern Design
The simplified rectangular pattern pieces nest together easily. And since structure mapping can compensate for small size differences, the rectangles can be further adjusted to fit together without empty spaces.
The only drawback is that the pattern cannot be used with standard fabric, since the crucial shaping elements in the shoulders, collar, sleeves, etc. are excluded.
Compositing Structures
With structure-mapped knitting, it is possible to locally change the size of the fabric. Using distinct colours for each structure size, the zero-waste pattern is subdivided to reshape it into the original pattern.
To validate the distribution of structures, the pattern is simulated in CLO3D and compared to the original jacket. Unfortunately, CLO is not made for this kind of simulation, resulting in wrinkles that do not exist in the actual material.
Step 4: Production
Knitting, Felting, and Sewing
On a Stoll CMS 530, I knitted the entire fabric independently from ultra-fine merino wool. This yielded a semi-shaped knitted textile, which I felted to create the desired material for an overcoat. All seams were cover stitched for durability and most fabric edges were untreated because the felting process locked the yarn in.